Steel Buildings Oklahoma offer many benefits for commercial, industrial and residential applications. They are customizable, durable and can be built quickly, allowing for faster occupancy and saving money on construction costs.
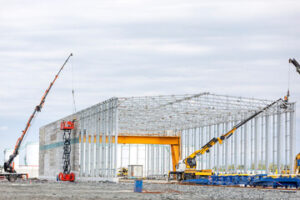
Frame columns support the back and front walls of a steel building, connecting to eave rafters above. They also provide framed openings for doors and windows.
Steel is known as one of the strongest construction materials. Its strength gives steel buildings durability and helps them stand up to natural disasters. It also makes them less likely to be damaged by lightning. When a steel building is struck by lightning, the electricity is dissipated and not concentrated at a single point. Steel is also less susceptible to rust, mold and mildew that can cause damage over time.
Steel buildings are constructed using pre-engineered components and can be built at a much faster pace than traditional buildings. This type of construction allows for more flexibility in design and layout, making it ideal for a variety of applications. Steel buildings are also more durable and can withstand greater loads than wood or concrete structures.
The first step in constructing a steel building is preparing the foundation. This can be done by pouring a concrete slab or pier/beam foundation, depending on the type of building. Once the foundation is prepared, the pre-engineered steel components are brought to the building site and assembled. These components include frame columns, end wall rafters, and eave struts. The eave struts provide structural support for the front and back of the building, while the end wall rafters connect to the frame columns above.
Steel buildings are often easier to assemble than wood-framed buildings, as all framing is measured, cut with a saw and connected with self-drilling screws. This type of construction can save a great deal of money and time, and it provides the added benefit of allowing for more floor plan options in the future. When choosing a steel building, be sure to consider the purpose of the building and its location, as these factors will help determine the size of your structure.
Durability
The durability of steel buildings comes from the precision engineering that goes into the building’s design. The blueprints are created using advanced software to optimize the structural integrity of the building, making it able to stand up to the forces that may be put on the structure throughout its lifetime. This makes metal buildings a great choice for warehouses, storage sheds, workshops and more. They’re fire-resistant, immune to wood rot and less vulnerable to pests than other types of structures.
Another aspect of their durability is the strength of the steel construction materials used. Unlike other framing materials, steel is inorganic and doesn’t absorb moisture content. This eliminates or significantly reduces rusting and mold issues, which can otherwise degrade the integrity of the building. Additionally, steel’s dimensional stability allows it to hold up in all directions, while other materials can expand and shrink, which can lead to long-term structural problems.
While the durability of steel buildings is a huge draw for many potential buyers, it’s important to know that they do require regular maintenance. To prevent the growth of fungus, mold and rust on the walls, regular cleanings should be performed. A low-pressure power wash, store-bought power washer cleaner or warm water with detergent works well for this purpose. It’s also important to immediately address any damage that occurs on the exterior of the building. This will help to protect the structural integrity of the building and keep it looking its best for years to come.
By following these simple maintenance tips, owners can ensure their steel building is in good condition for as long as they own it. They don’t require the massive upkeep that some other types of buildings do, but they still need to be supported and preserved.
Recyclability
In the construction industry, it’s important to use building materials that can be recycled and that help reduce environmental impact. Steel is the perfect material for this, and many of the buildings constructed using it are known to be eco-friendly.
Steel buildings are constructed with fewer resources than traditional brick or wood structures, and their construction times are often faster. This is because the pre-engineered components are designed to be easy to assemble on-site, reducing labor costs and overall project timelines.
It takes more than 20 years for a single tree to grow enough to be harvested again for lumber, but steel can be used again and again without losing its strength. It also requires less energy to mill than other metals, so it’s more sustainable.
Most pre-engineered steel structures are designed to be eco-friendly, and many of them can easily be upgraded or expanded. They’re an excellent choice for self-storage facilities, for example, as people are increasingly looking to store their personal belongings in a safe and secure environment.
Moreover, it’s important to choose a contractor that’s experienced in working with pre-engineered steel structures. Look for a company with an impressive portfolio of past projects and be sure to ask for references. This will give you insight into the contractor’s reliability, level of experience and commitment to customer service.
Steel buildings are also incredibly eco-friendly, as they’re 100% recyclable. The steel used to make a new metal building can be reused countless times without losing its strength, making it the most recyclable building material on the planet. LGS framing, for instance, contains a minimum of 25% recycled steel. This makes it an eco-friendly option that’s recognized as such by the Leadership in Energy and Environmental Design (LEED) green point system.
Energy Efficiency
Steel is a natural insulator, keeping heat inside during the winter and cutting energy costs in the summer. In addition, the straight framing commonly used in steel buildings eliminates sagging and warping over time, further increasing energy efficiency. Finally, a steel building is less susceptible to damage from fires and floods than other types of buildings, further decreasing the need for repairs or replacement.
The energy efficiency of steel buildings is increased by several factors, including the use of high-quality insulation materials, efficient ventilation systems, and daylighting solutions. These innovations in construction technology and design can significantly reduce the demand for energy-intensive heating and cooling, resulting in significant cost savings over the lifetime of the building.
Many of these energy-efficient features can be added to existing steel buildings. For example, adding ridge vents to the roof of a steel building can improve air circulation, lowering indoor temperatures and reducing reliance on HVAC systems. Similarly, adding skylights and windows can improve natural lighting, minimizing the need for artificial lighting during the day.
Adding solar panels can further reduce a building’s reliance on traditional energy sources, reducing carbon emissions and saving on electricity bills. Additionally, wind energy systems can be installed in windy locations to supplement energy needs.
Energy efficiency can also be improved with regular maintenance of steel buildings, such as inspecting and repairing HVAC systems to ensure they are properly sized for the space and keeping up with maintenance tasks like cleaning the coils and replacing filters. In addition, a reflective coating on the outside of the building can help to reduce sun exposure and keep the interior of the building cooler in the summer.
Flexibility
Steel buildings are flexible enough to accommodate a wide range of purposes. They are easy to customize and provide plenty of space for all types of manufacturing operations. They are also suitable for warehouses, office buildings, retail spaces, and more. In addition, they can be adapted to fit specific needs and meet environmental standards. They are easy to transport and can be constructed on any site.
When designing a steel building, it is important to plan ahead and prepare for all the steps involved in construction. This will ensure a smooth and efficient project. It is also important to choose a contractor with experience in metal building construction. Ask contractors about the projects they have completed and look for online reviews. These will give you an idea of their reliability and quality of work.
Another important factor in building a steel building is choosing the facade. Some communities have strict building codes that you must adhere to, while others may require a specific color or materials. Depending on the location, you can choose between brick, masonry block, curtain walls, or metal panels. It is also important to consider the weather conditions in your area and plan accordingly.
Many businesses are looking for flexibility in their commercial space. They need to be able to accommodate changing customer demands, as well as expand when necessary. Steel buildings are a great option for businesses that need to change their interiors frequently.
Since steel buildings are easy to assemble and can be built in less time than traditional building, they are a good choice for construction companies that need to meet deadlines. They are also easier to relocate than conventional buildings, making them an ideal solution for expanding business operations.